Balanced Cantilever Construction of Precast Segmental Bridges
Introduction
Balanced cantilever construction is a widely used method for building precast segmental bridges. This technique offers several advantages, including reduced construction time, minimal environmental impact, and enhanced structural efficiency. In this blog, we will explore the principles, advantages, challenges, and practical considerations associated with this construction method.
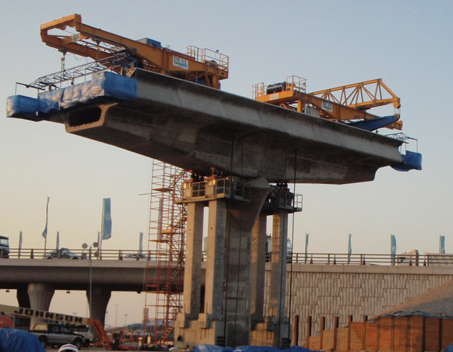
What is Balanced Cantilever Construction?
Balanced cantilever construction involves assembling bridge segments in a cantilever manner from a central pier or support. The segments are precast, meaning they are manufactured off-site and transported to the construction site. The method derives its name from the fact that segments are added to both sides of the pier in a balanced fashion, which maintains structural equilibrium during construction.
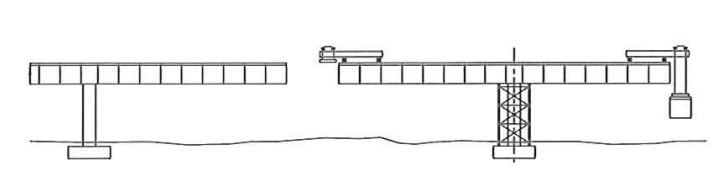
Key Components
- Precast Segments: These are the individual sections of the bridge, typically made from reinforced concrete. Each segment is designed to interlock with adjacent segments, providing structural integrity. Shape of Deck section depends on carriageway width but can have multiple box girder for one carriageway. Various option of deck can be chosen such as double cell box girder or single cell box with transverse ribs, single cell box with struts or parallel single cell box. limits of segment weight and size are decided based on option of erection equipment and transport vehicle available for the project. Deck section is not only designed for permanent loading but also the temporary loading such as lifting points during erection.
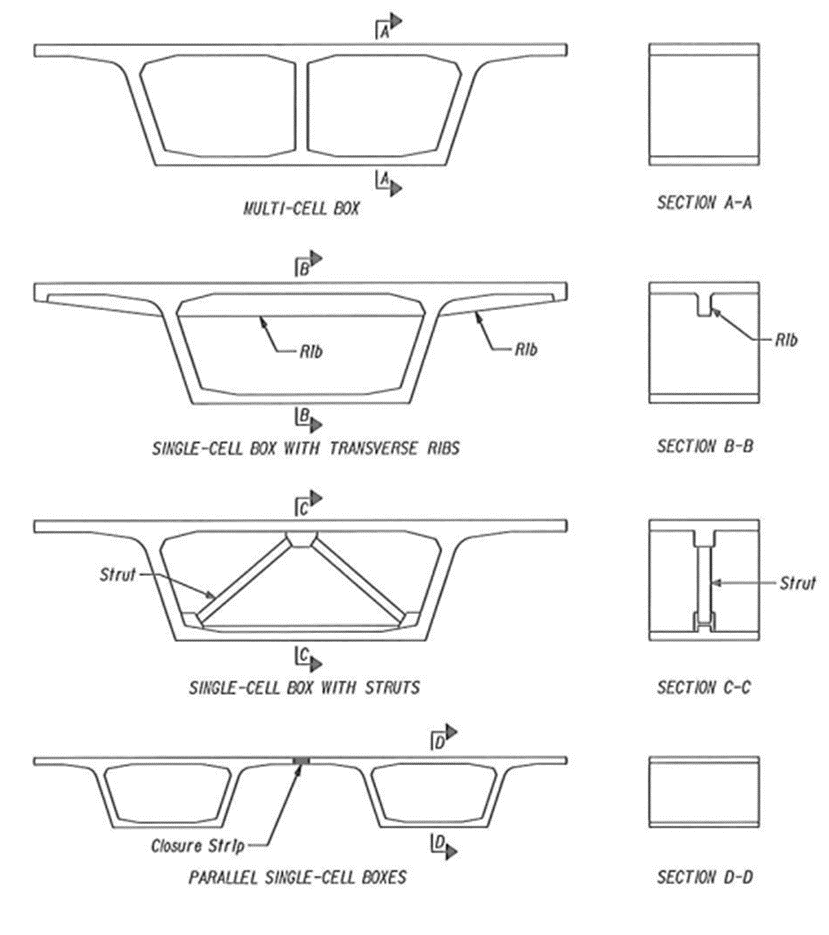
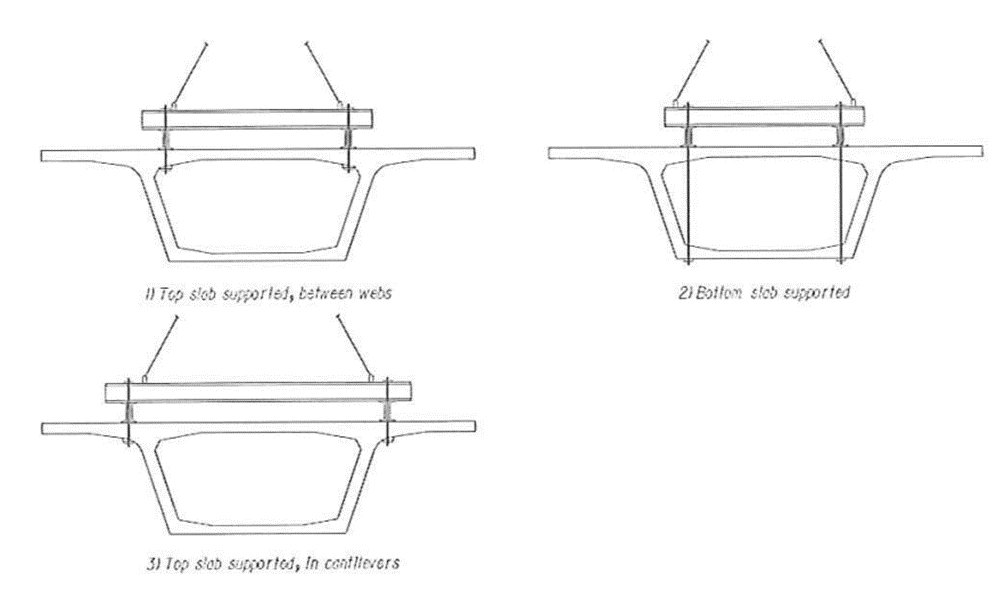
- Piers: These vertical supports are critical for balancing the cantilevered segments. They must be designed to withstand the bending moments and shear forces that arise during construction and use.
- Cantilever Arms: As segments are added, they extend outwards from the piers. The length of these arms is carefully calculated to maintain balance.
- Temporary Supports: Often used during the initial stages of construction to support the segments until enough weight is added to create balance.
Advantages of Balanced Cantilever Construction
- Speed of Construction: The use of precast segments allows for rapid assembly on-site, reducing overall project duration.
- Minimal Site Impact: Since much of the work is done off-site, there is less disturbance to the surrounding environment. This is particularly beneficial in sensitive areas.
- Reduced Material Use: The method can lead to material savings as the structural efficiency of cantilevering reduces the need for excess concrete.
- Flexibility: The method can accommodate various bridge shapes and spans, making it suitable for a wide range of projects.
- Safety: Working with precast elements can reduce on-site risks associated with wet concrete pouring, especially in challenging environments.
Challenges in Balanced Cantilever Construction
Despite its advantages, balanced cantilever construction does come with challenges:
- Complex Design: The design of balanced cantilever bridges can be intricate due to the need to ensure equilibrium during construction. Engineers must carefully calculate segment weights and the timing of their placement.
- Transport and Handling: Precast segments can be heavy and cumbersome, requiring specialized transportation and handling equipment. This may increase logistical complexity.
- Quality Control: High-quality manufacturing of precast segments is crucial. Any defects can lead to significant issues during assembly and long-term performance.
- Weather Dependence: Construction can be sensitive to weather conditions, particularly during segment lifting and positioning.
Construction Process
1. Planning and Design
The first step involves comprehensive planning, including site analysis, structural design, and construction sequencing. Engineers must determine the size and shape of segments and the location of piers based on traffic load requirements and environmental conditions.
2. Fabrication of Precast Segments
Segments are casted in a controlled environment using either short line method or long line method in casting yard based on available yard space and ground condition. In Short line method, segment is casted between the bulkhead template and match cast segment and once segment is casted it is used as match cast segment in the next stage of casting. In Shortline method, formwork remain in place as shown in below snapshot and casted segments are moved forward for next stage. In long line method, all segments are casted side by side in one line following the accurate alignment as per design. here casted segment remains in place while formworks are moved in forward direction of casting stages. All casting joints are having Quality assurance measures are crucial to ensure that each segment meets design specifications. Bulkhead template is used for casting the joint shape of the segments. Web shear keys are provided to have full shear transfer at joints. Alignment keys at top and bottom slab of deck are for setting proper alignment of deck. Duct for permanent tendons and temporary PT bar are present for each segment.
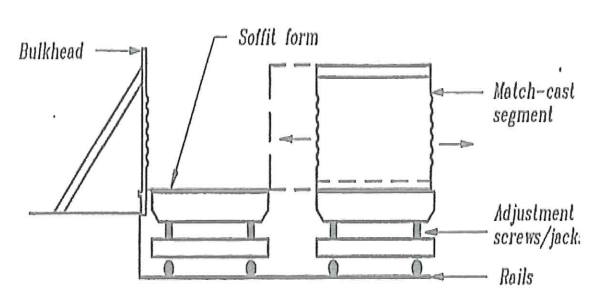
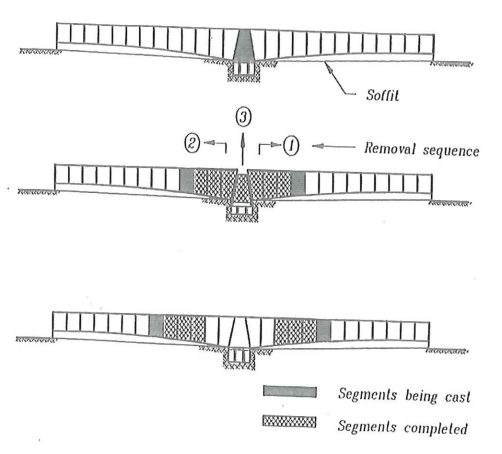
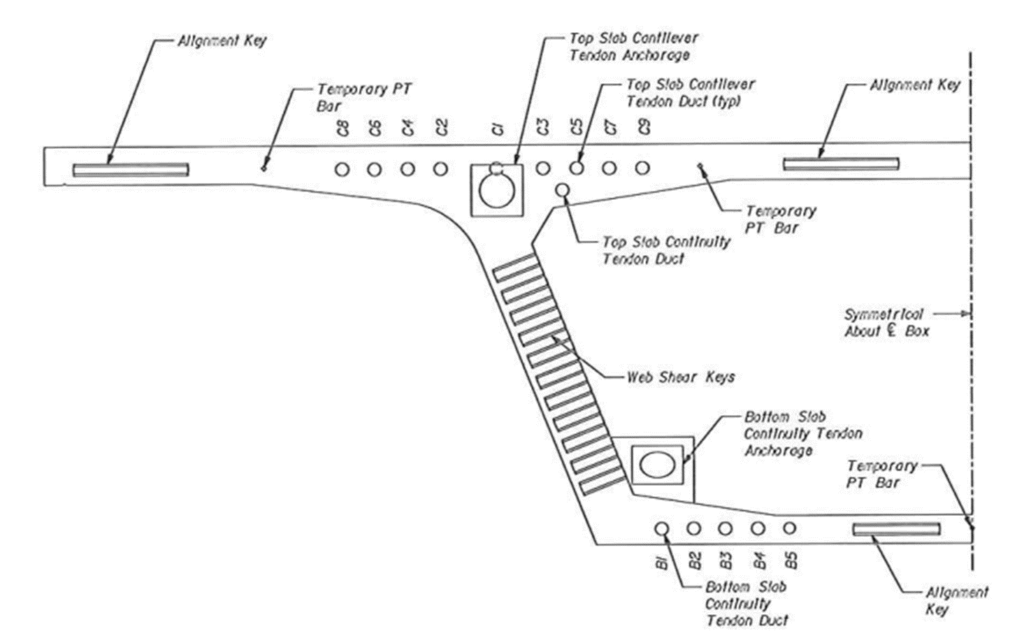
3. Construction of Piers and pier segment
Piers are constructed using traditional methods. Temporary supports may be installed to aid in the balancing act of the cantilevered segments.

4. Erection of deck Segments
Segments are lifted and positioned onto the piers, starting from the center and moving outward. Careful monitoring ensures that each addition maintains balance. Temporary PT bars are stressed with 50% GUTS to have maximum clamping force of 0.3 MPA. Alignment keys of top and bottom slab are used for alignment of segments.
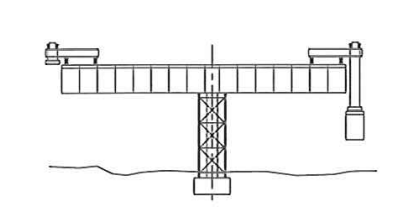
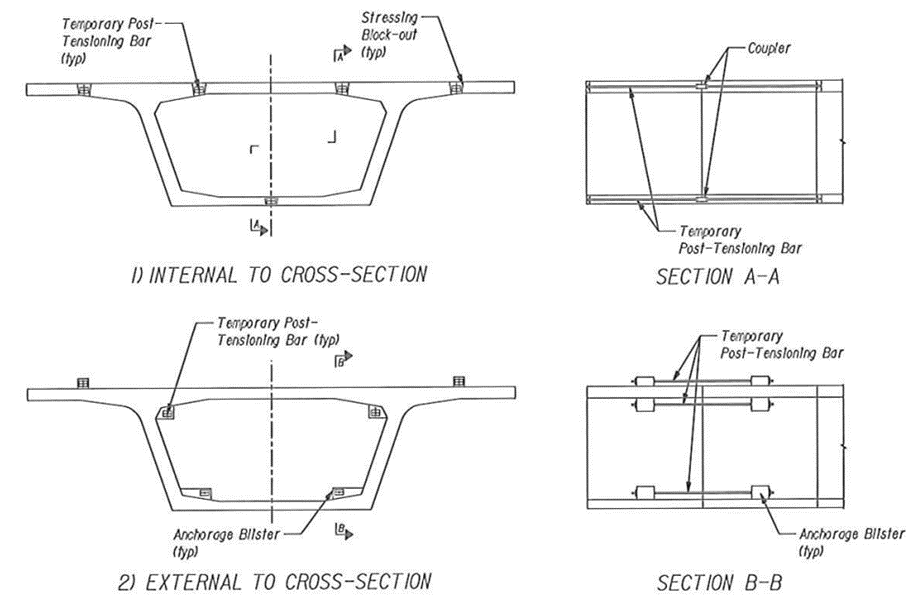
5. Post-Tensioning
Once segments are in place, post-tensioning cables are installed to enhance structural integrity. This process involves tensioning the cables to compress the concrete, increasing the bridge’s load-bearing capacity.
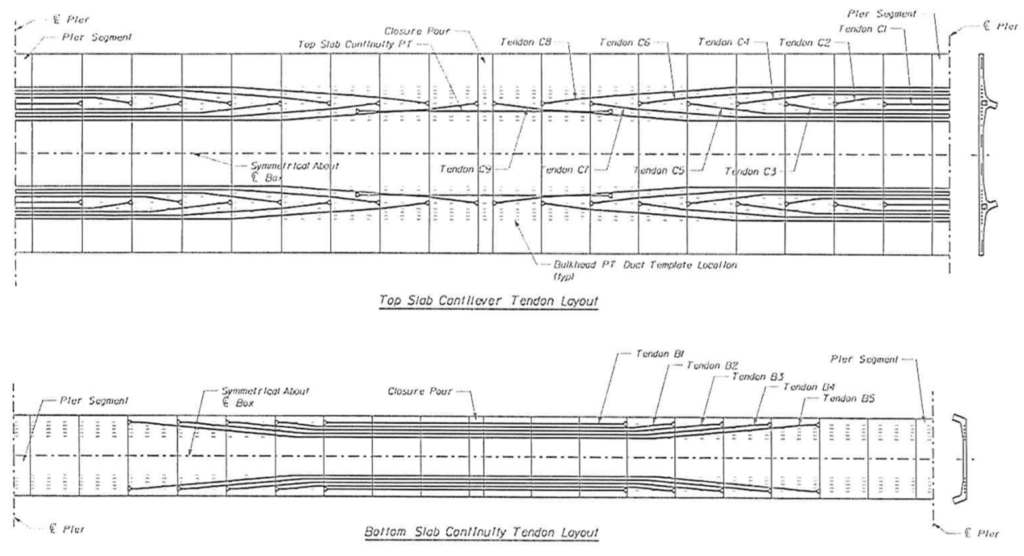
6. Finishing Works
Finally, the bridge undergoes finishing works, including paving, installation of safety features, and aesthetic enhancements.
Conclusion
Balanced cantilever construction of precast segmental bridges is a sophisticated and efficient method that offers numerous benefits for modern infrastructure projects. While it presents certain challenges, careful planning, quality control, and innovative engineering practices can mitigate these issues. As transportation needs continue to evolve, this construction method will likely play an increasingly vital role in building durable and sustainable bridges.
For engineers and project managers, understanding the intricacies of this technique is essential for successfully navigating the complexities of modern bridge construction.
Great weblog here! Also your web site lots up very fast! What host are you the usage of? Can I am getting your affiliate hyperlink for your host? I want my web site loaded up as fast as yours lol.